Efficient Distillation Process: Heating Crude Oil Pipes with Induction Technology.
The distillation process plays a crucial role in refining crude oil into valuable products such as gasoline, diesel, and jet fuel. Traditionally, heating crude oil pipes for distillation has been done using conventional methods, which can be time-consuming and energy-inefficient. However, with the advent of induction technology, a more efficient and precise heating method has emerged. In this blog post, we will explore how induction technology is revolutionizing the distillation process by heating crude oil pipes effectively, resulting in improved productivity, energy savings, and overall process efficiency.
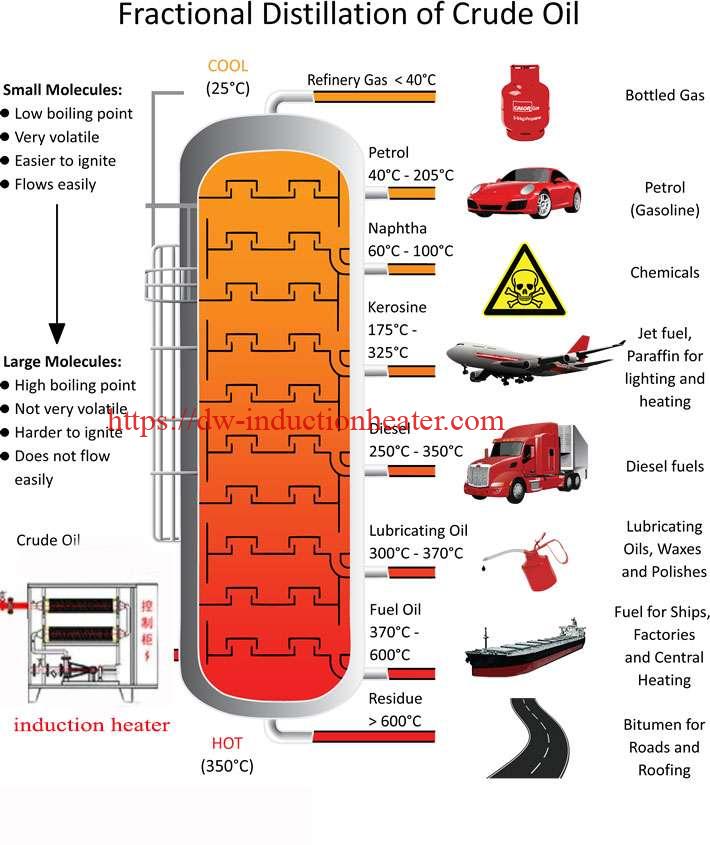
1. Understanding the distillation process in oil refining
Understanding the distillation process is crucial in oil refining, especially when it comes to heating crude oil pipes with induction technology. Distillation is a key step in the refining process that separates crude oil into different components based on their boiling points. The process involves heating the crude oil to vaporize it and then condensing the vapor back into liquid form to extract various products such as gasoline, diesel, and jet fuel.
In oil refining, the distillation process typically involves a series of distillation columns or towers, each designed to separate specific fractions of crude oil based on their boiling points. As the crude oil is heated, the lighter components with lower boiling points rise to the top of the column, while the heavier components with higher boiling points sink to the bottom.
Heating crude oil pipes with induction technology offers several advantages in the distillation process, such as precise and efficient heating, reduced energy consumption, and improved safety. Induction heating uses electromagnetic induction to generate heat directly within the material being heated, resulting in faster and more uniform heating compared to traditional methods.
By understanding the distillation process in oil refining and utilizing induction technology for heating crude oil pipes, refineries can optimize their operations, improve product quality, and enhance overall efficiency in the production of valuable petroleum products.
Â
2. Introduction to induction heating technology
Â
Induction heating technology is a cutting-edge method that has revolutionized various industries, including distillation processes in oil refining. This innovative technique utilizes electromagnetic induction to generate heat within a conductive material, such as metal pipes used in the distillation of crude oil. By applying high-frequency alternating current to a coil surrounding the pipe, induction heating induces electrical currents that result in rapid and precise heating of the pipe’s surface. This localized heating is highly efficient, as it minimizes heat loss to the surrounding environment and allows for targeted heating of specific sections of the pipe as needed. As a result, induction heating technology offers enhanced control, energy efficiency, and speed in heating crude oil pipes during the distillation process, ultimately leading to increased productivity and cost savings for oil refineries.
Â
3. Benefits of using induction technology in heating crude oil pipes
Â
Using induction technology to heat crude oil pipes offers numerous benefits that can significantly improve the efficiency of the distillation process. One of the key advantages is the ability to achieve precise and uniform heating throughout the pipes, resulting in consistent temperatures and reduced energy consumption. Induction technology also enables rapid heating, which helps to shorten the heating process and increase overall productivity.
Furthermore, induction heating is a clean and environmentally friendly method that does not involve direct contact between the heating source and the pipes, reducing the risk of contamination and ensuring a safe working environment. Additionally, this technology offers excellent control over the heating process, allowing for adjustments in real-time and minimizing the chances of overheating or uneven heating.
Moreover, induction technology is highly reliable and requires minimal maintenance, leading to cost savings and improved operational efficiency. The overall performance and longevity of the crude oil pipes can also be enhanced by utilizing this advanced heating method. In conclusion, the benefits of using induction technology in heating crude oil pipes make it a valuable asset in achieving an efficient distillation process.
Â

Traditional crude oil distillation methods involve heating the oil in large vertical columns known as distillation towers. As the oil is heated, its components vaporize and rise to different levels within the tower, where they are collected and condensed. However, this process is not without its drawbacks.
One of the major challenges is the uneven heating of the crude oil. Due to the size and shape of the distillation towers, the heat distribution is often inconsistent, leading to inefficiencies in the separation process. This results in lower distillation yields and higher energy consumption, ultimately impacting the overall profitability of oil refineries.
Another challenge is the slow heating and cooling rates associated with traditional distillation methods. The gradual heating and cooling cycles not only prolong the distillation process but also contribute to increased maintenance costs and downtime.
How Induction Heating Improves Distillation Efficiency
Induction heating technology offers several advantages over traditional distillation methods, leading to enhanced distillation efficiency. Firstly, the uniform heating provided by induction heating ensures consistent temperature distribution throughout the crude oil, minimizing the formation of hotspots and cold spots. This promotes better separation of the oil components and improves distillation yields.
Secondly, induction heating enables precise and rapid heating and cooling cycles, significantly reducing the overall distillation time. This not only increases productivity but also minimizes energy consumption and maintenance costs. The ability to achieve higher heating rates also allows for better control over the distillation process, leading to improved product quality.

Additionally, induction heating systems can be easily integrated into existing distillation setups, making it a cost-effective solution for oil refineries. The flexibility of induction heating technology allows for customization based on specific refinery requirements, ensuring optimal performance and efficiency.
Case Studies of Successful Implementation of Induction Heating in Crude Oil Distillation
Several oil refineries have successfully implemented induction heating technology in their crude oil distillation processes, reaping the benefits of improved efficiency and productivity. One such case study involves a refinery in Texas that experienced a significant increase in distillation yields after installing an induction heating system. The refinery reported a 15% increase in product output and a reduction in energy consumption by 20%.
Another case study comes from a refinery in the Middle East, where induction heating was introduced to replace traditional heating methods. The refinery saw a drastic reduction in distillation time, resulting in higher production rates and improved profitability. The installation of the induction heating system also led to a decrease in maintenance costs and a more sustainable refining process.
These success stories highlight the transformative impact of induction heating technology on crude oil distillation, making it a compelling choice for refineries looking to enhance their efficiency and profitability.
Â
Factors to Consider When Choosing Induction Heating for Crude Oil Pipes
When considering the implementation of induction heating in crude oil distillation processes, there are several factors to take into account. Firstly, the size and capacity of the distillation setup should be evaluated to determine the appropriate induction heating system. Factors such as pipe diameter, material composition, and flow rate should be considered to ensure optimal performance.
Secondly, the reliability and durability of the induction heating equipment should be a priority. It is essential to select a reputable manufacturer with a proven track record in the industry. Additionally, the maintenance requirements and availability of spare parts should be taken into consideration to minimize downtime and ensure uninterrupted operation.
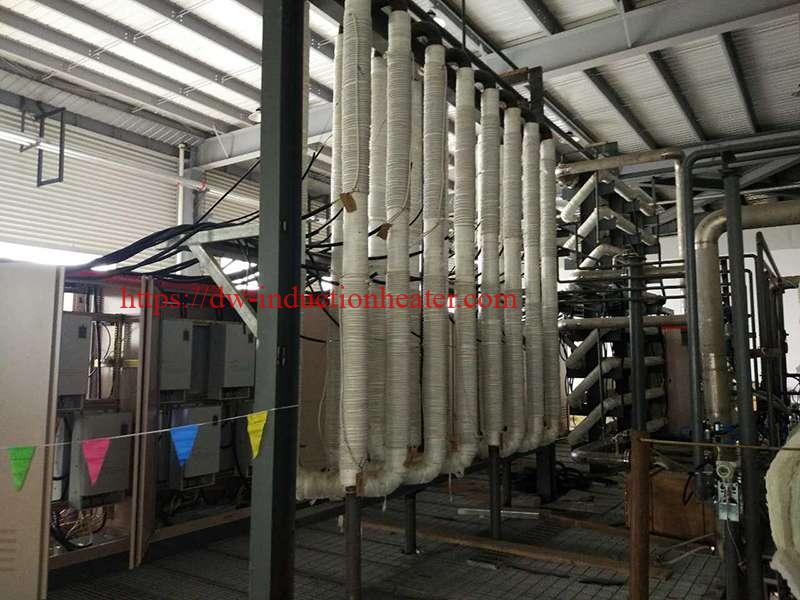
Furthermore, safety measures should be carefully assessed when integrating induction heating technology into existing distillation setups. Adequate insulation, grounding, and temperature monitoring systems must be in place to prevent accidents and ensure the well-being of refinery personnel.
Conclusion
Induction heating technology offers a compelling solution to enhance the distillation efficiency of crude oil pipes. By providing uniform heating, faster heating and cooling cycles, and improved control over the distillation process, induction heating systems can significantly improve distillation yields, reduce energy consumption, and increase profitability for oil refineries.
The successful implementation of induction heating in crude oil distillation has been demonstrated through various case studies, showcasing the transformative impact of this technology. Factors such as system selection, installation, and maintenance should be carefully considered to ensure optimal performance and reliability.
The cost and energy savings associated with induction heating further contribute to its appeal, along with the potential for future advancements and innovations in the field. As the petroleum industry continues to evolve, induction heating technology will play a crucial role in driving efficiency, sustainability, and profitability in crude oil distillation processes.