PDF handbook of induction heating eddy current
Both induction heating and eddy current testing work with coils, generators, ac-current and ac-voltage,
frequencies, field strength and induction law. Contrary to heating of the test parts, the eddy current
test does not want to heat the parts at all but wants to examine them for their metallurgical microstructure, thus for their mechanical features like hardness, case depth or alloy. The eddy current test
does not provide absolute values (e.g. “56 HRC” or “2.6 mm case depth”).
The eddy current test does detect fine differences in micro-structure with high sensitivity. In the
production line, within a fraction of a second, a non-destructive 100 % test for
โข hardness
โข case depth
โข hardness run out, hardness pattern
โข tensile strength
โข carbon content
โข soft spots
โข surface decarburisation
is completed, and thus quick corrective reactions to any variance from the specified structure can be
realized. With a suitable mechanical part handling arrangement, the transport from the hardening
station to the test station takes only a few seconds. Faulty parts, caused by a damaged inductor, a
jammed quench nozzle or an unknown reason are immediately detected, providing an enormous
savings in time and costs!
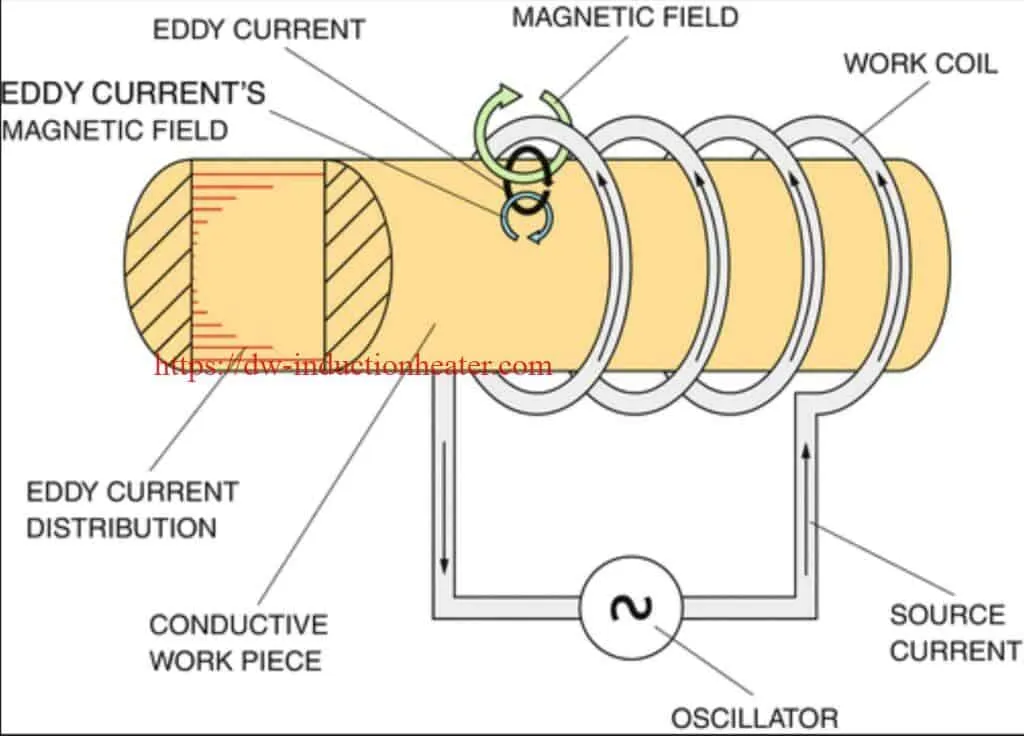
Different from the induction heating, the energy for eddy current testing is very small, in the milliwatt
range. Field strength is low and permeability is in the range of the initial permeability. Test frequencies
ranging from some Hz to some hundreds of kHz provide information on undesired structures via the
frequency dependent penetration depth of the eddy current and on the formation of permeability. Very
small electrical signals require a very precise evaluation in order to assure their differentiation from
ambient interferences. A small drift from variation in temperature and high long term stability are
absolutely necessary. Digitization of input voltages immediately at the front end of the electronic
evaluation is of huge advantage.